新しい木材ガス化CHPユニットの特徴
電気出力で5MWくらいの木質バイオマス発電所でも、蒸気ボイラ・蒸気タービン方式に依拠する限り、25%程度の発電効率しか得られない。その一方で、木質燃料をガス化して、ガスエンジンやガスタービンで発電する方式であれば、理論的には35%程度の効率が得られるはずである。そのため過去2、30年来後者の研究開発が世界中で進められてきたが、目を見張るような技術は出てこなかった。
何が技術開発のネックになっていたのか。そして近年彗星のごとく出現した小型のCHPユニットは、このネックをどのようにして克服したのか。それが今回のテーマである。
木材ガス化発電の二つの難関
とりあえず図1を見ていただきたい。上段にあるのが通常の火力発電方式である。すなわち、木質バイオマスを燃焼させた熱で高温高圧の蒸気をつくり、その蒸気でタービンを回して発電することになる。図でタービンのところから出ている熱は発電排熱で、これをうまく使えば、熱電併給つまりCHPになる。ただしこの方式を採択できる下限は電気出力で2MW、無理をして1MWほどだから、どのみち小型のCHPには向いていない。
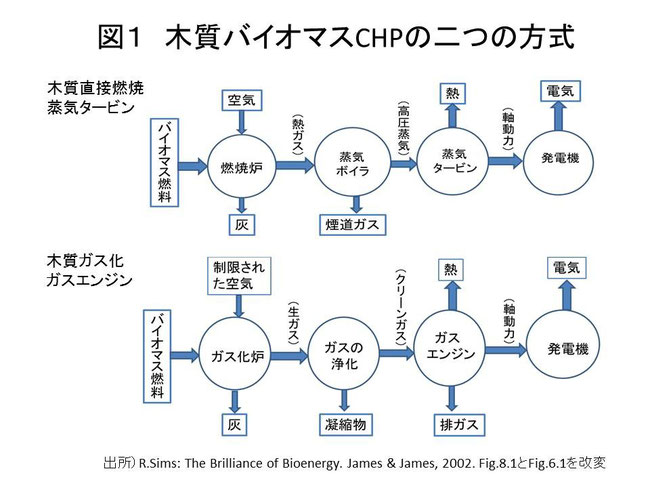
下段がガス化発電である。30kWとか50kWの出力でも変換効率を25%くらいまで引き上げることができ、小型のCHPには適している。ガス化炉に燃料を詰め、送り込む空気量を制限しながら熱を加えていくと、一酸化炭素、水素、メタンなどを含む「生ガス」(燃料ガス、木ガス)が出てくる。このガスはいわば汚れたガスで、そのまま燃やして温水や蒸気を得ることはできが、ガスエンジンやガスタービンには入れられない。タールのような不純物(凝縮物)を除去してクリーンなガスに変える必要がある。
木材のガス化自体は100年も200年も前から行われてきた。1850年代のロンドンで「木ガス」によるガス灯が灯った。1904年には木ガスの自動車が走っている。しかしバイオマスのガス化で、成分の安定したガスを取り出すのは容易ではない。送り込む空気量と炉内温度によってガスの組成が大きく変わり、さらにバイオマスの種類、水分率、チップの形状によっても微妙に変化する。これらの要件のすべてがきちんとコントロールされていないと、成分の安定した生ガスは得られない。
第二の難関はガスの浄化である。クリーニングの方法にはいくつかあり、それをうまく組み合わせて不純物を除去しているのだが、これが予想以上に厄介な作業である。木質燃料で生ガスをつくったものの浄化ができず、発電機を回せないまま失敗した事例は数限りなくある。
課題の多い既存のガス化発電プラント
もちろん長期にわたって運転しているガス化発電の事例がないわけではない。前回言及したObernbergerらの報告では4つ挙げられているが、筆者が実地で見たのはこのうちの二つだ(前稿の表1のガス化プラント③と④)。出力は2MWと4.5MWで比較的大きい。これらがどのようにして難関の克服に立ち向かっているか、簡単に述べておこう。
デンマークのハーボアにあるVølundのバイオマスガス化プラントは1993年に熱出力4MWの地域熱供給施設としてつくられた。2000年に1MWのガスエンジンが2基入り、それ以来CHPの運転を続けている。アップドラフトのガス化炉であるため、燃料チップの大きさや水分率については、それほどうるさくない。その代り大量のタールが出る。このプラントでのガスの浄化方法は長年の経験で習得した「職人芸」で、現地で会った専門家は「機械だけ日本へ持って行っても動かないよ」と忠告してくれた。
よく知られたもう一つの例は、オーストリアのギュッシングにあるバイオマスガス化プラントである。2001年から稼働している。構造はかなり複雑で、ガス化炉には流動床が二段構えで入っている。ガス化ゾーンに蒸気駆動のバブリング流動床、燃焼ゾーンに空気駆動の循環流動床。またガス冷却装置などから出る排熱でORCタービンを動かし、発電効率を高める仕組みもある。ウィーン工科大学の専門家たちが知恵を絞って、さまざまな技術を導入したのであろう。これほど構造が複雑になると設備費が膨らむから、出力を相当大きくしないと採算が取れない。現在このプラントは運転を止めているという情報もある。
小型ガス化ユニットの技術的な特徴
いずれにせよ、ハーボアやギュッシングにあるガス化プラントは称賛されるけれど、見倣おうとする者はほとんど出てこなかった。そのような中でSpanner社とBurkhardt社の小型CHPユニットが短い期間内に100基も200基も設置されるというのは大変なことである。前回見たように、1年を通して7000時間、8000時間安定して稼働することと、量産による資本コストの低減に成功したことが大きい。
ここでは二つのユニットの技術的な特徴を一瞥しておこう。Spanner社のガス化炉は教科書的に言うと、ダウンドラフトの固定床である(図2の左側)。燃料の木質チップは上から投入される。火が燃えているのは燃焼層で、炉の上のほうは温度が低い。燃料は100℃前後の乾燥層を通り、乾留層(300℃)で熱分解が起こる。ここで発生する高分子の炭化水素(タール類)は高温(1400℃くらいになる)の燃焼層で燃やされ、次の還元層で可燃ガスに変換される。
ダウンドラフト方式の利点はタール分の少ない燃料ガスが得られることだ。その代り良質の木質チップを要求する。水分率は15%以下で形がそろっていることが望ましい。粉状のものが多いと、ガスが上から下へスムーズに流れなくなるからである。Spanner社のユニットはこの要件を忠実に守っている。
従来の常識を破ったのはBurkhardt社のペレット焚きのユニットである。ガス化炉のタイプとしては「アップドラフトの固定床」と「流動層方式」を統合したものだという。燃料となるペレットはガス化炉の下から押し上げられて、乾燥層、乾留層、燃焼層を通過してガス化されるのだが、ここまでは通常のアップドラフトの固定床と変わらない。ところが最上部の還元層では燃焼後の気体物質が渦巻き状に撹拌されるなかで、タール分がきれいに分解される。
ガス化炉自体は一段階のごく単純な構造だが、分散板も付けないでスムーズにガス化が進展するのは、炉に付けられたいくつものセンサーと制御システムが、燃料、ガス化剤(予熱空気)および生成ガスの混合割合と送り速度を正確にコントロールしているからである。
この制御システムがうまく機能するためには、良質のペレットを使うことが必須の条件となる。チップに替えてペレットを使うと、ユニットの構造が大幅に単純化され、その分設備投資も節約されることになった。
楽しみな今後の展開
筆者が木質エネルギーの世界に足を踏み入れたのは今から約20年前の90年代前半のことだが、当時話題になっていたのはバイオマス統合ガス化コンバインドサイクル(BIGCC)と呼ばれる発電方式である。まず木材をガス化してガスタービンを回し、その排熱で蒸気タービンを駆動させて二段構えで電気をつくるというものだ。そのお蔭で発電効率が高まり、40%は堅いと言われていた。実証実験用のパイロットプラントが世界の各地で計画され、Biomass
& Bioenergyという専門誌が10か所ほどの事例を集めて特集号を発刊したほどである。このうちの2、3のプラントだけが短期間運転されたが、どれも長くは続かなかった。
それ以来バイオマスガス化発電への期待は次第にしぼんでいく。筆者も半ば見切りをつけていた。それが2012年になってドイツからニュースが入り、翌13年の夏にドイツ南部の町ブンジーデルを訪ねてBurkhardt社のCHPユニットを始めてみた。一番に驚いたのはコンパクトにまとめられた外観の美しさである(図3)。小型ガス化炉と言えば、タールで黒く汚れた鉄の容器を連想するが、むしろ洗練された電化製品を思わせる。運転音も静かで、年中休むことなく黙々と電気と熱を生産し続ける健気さに一種の感動さえ覚えたものである。170kWの電気出力でありながら、発電効率30%強、熱を含む総合効率75%というのは立派なものだ。
バイオマスガス化発電は巨大なBIGCCには失敗したが、ごく小型のCHPでうまくいきそうな気配になってきた。そのための要件を整理すると次のようになる。
- 乾燥チップやペレットのような質の高い木質燃料に特化すること
- ガス化炉や浄化の装置は選択した燃料に特化したコンパクトな構造にすること
- 各種のセンサーを要所に付けてガス化プロセスの自動制御を図ること
- 量産による設備費の削減が見込めること
こうした要件を満たそうとすると、自然と500kW以下の小型のものになってしまうのかもしれない。フィンランドの技術研究センター(VTT)が開発したVolter社のCHPユニットも30kWと40kWの2種類である(図4)。こちらはSpannerと同じチップ焚きのダウンドラフト方式だが、特徴としては出力制御の幅が広いことと、余った電気が蓄電できることである。Burkhardt社と輸入契約を結んだ三洋貿易㈱がVolter 40も取り扱うとのことだ。選択できる機種の幅は確実に広がっている。各々の特徴をしっかりと押さえて、現場に合った最適な機種を選ぶようにしたい。
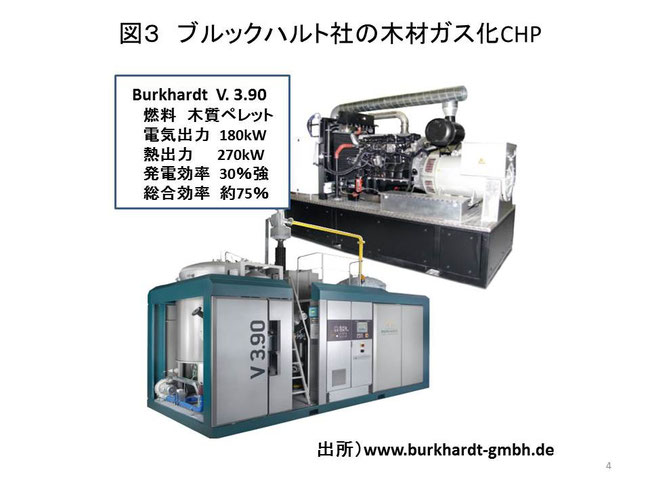
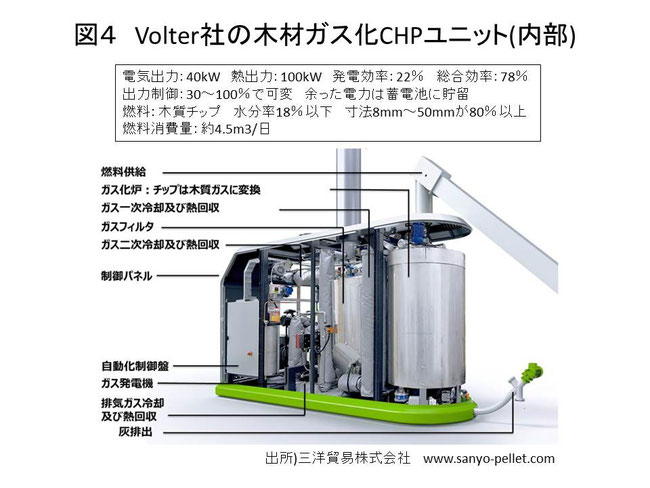